Essential Guide to **OSHA H2S Training**: Ensuring **Safety in the Workplace**
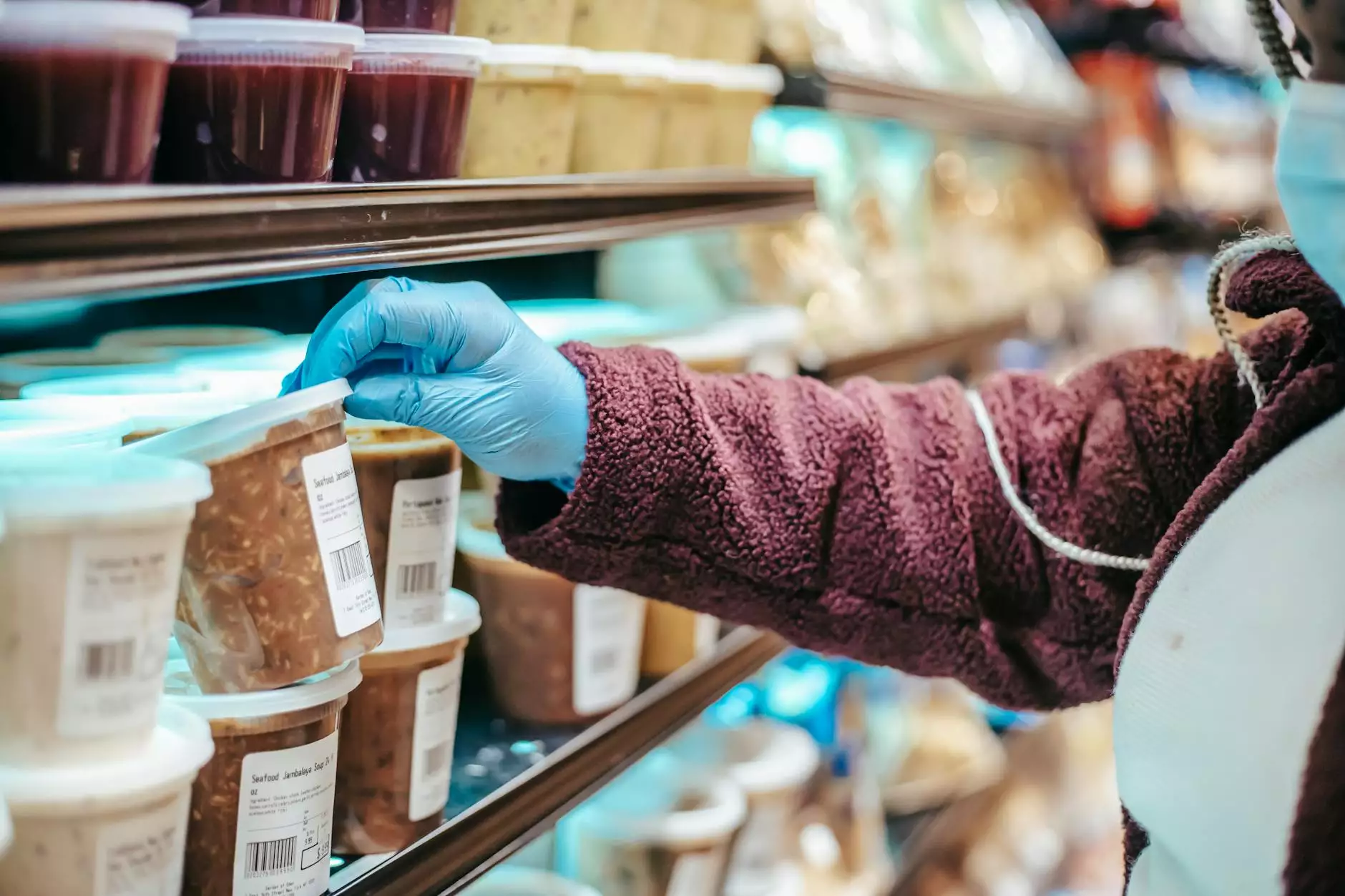
Working in environments exposed to hydrogen sulfide (H2S) gas poses significant health risks to employees. OSHA H2S training is a critical aspect of workplace safety, focusing on educating workers about the dangers of H2S and equipping them with the knowledge to respond effectively in hazardous situations. In this comprehensive guide, we will discuss the importance of H2S training, the specific training requirements set by OSHA, the benefits of proper training, and how to implement an effective training program within your organization.
Understanding Hydrogen Sulfide (H2S)
Hydrogen sulfide is a colorless gas known for its characteristic rotten egg smell. This highly toxic substance can occur in various industries, particularly in oil and gas extraction, sewage treatment, and mining. The primary risks associated with H2S include the potential for rapidly inducing unconsciousness, respiratory failure, and even death. Understanding its properties and effects is crucial for all employees working in potentially contaminated environments.
The Dangers of H2S Exposure
Exposure to H2S can lead to several health effects, some of which may become apparent immediately, while others can be delayed:
- Low Concentrations: At low levels (up to 10 ppm), H2S can cause irritation of the eyes, nose, and throat.
- Moderate Concentrations: At moderate levels (20-100 ppm), symptoms can include headache, dizziness, and nausea.
- High Concentrations: At concentrations above 100 ppm, H2S can incapacitate a person in seconds and lead to loss of consciousness, respiratory failure, or death.
The Role of OSHA in Hydrogen Sulfide Safety
The Occupational Safety and Health Administration (OSHA) plays a vital role in enforcing safety regulations for workers exposed to hazardous substances, including H2S. The primary regulation regarding H2S is outlined in OSHA standard 29 CFR 1910.1000, which sets permissible exposure limits (PEL) and requires employers to implement safety protocols.
Key OSHA Requirements for H2S Training
Under OSHA regulations, employers must provide training to workers about the hazards of H2S. Key requirements include:
- Identification of H2S Hazards: Workers must be trained to identify where H2S may be present in their work environment.
- Proper Use of Equipment: Employers must ensure employees are trained in the correct use of personal protective equipment (PPE) and gas detection systems.
- Emergency Response Procedures: Employees should be well-versed in emergency procedures and evacuation routes in case of H2S exposure.
- Regular Training Updates: OSHA requires ongoing training and refreshers to ensure that employees retain vital safety information.
Benefits of OSHA H2S Training
Implementing a robust OSHA H2S training program offers numerous benefits to both employers and employees:
- Enhanced Safety: Training significantly reduces the risk of H2S exposure incidents, protecting employee health and safety.
- Compliance with Regulations: Proper training ensures compliance with OSHA standards, which can help avoid legal issues and fines.
- Increased Awareness: Educated employees are more aware of their environment and can identify potential hazards before they lead to incidents.
- Cultivated Safety Culture: A commitment to safety training fosters a culture of safety within the organization, leading to improved morale and productivity.
Components of an Effective OSHA H2S Training Program
To create a successful training program, the following components should be included:
1. Comprehensive Training Materials
The training should include clear, concise materials that cover:
- Characteristics of H2S and its effects on human health.
- OSHA regulations and PEL for H2S.
- Personal protective equipment (PPE) requirements.
- Emergency response protocols and evacuation procedures.
2. Hands-On Training Sessions
Practical experiences, such as simulations or drills, allow employees to:
- Practice the use of gas detection equipment.
- Understand and demonstrate the proper use of PPE.
- Participate in emergency response exercises.
3. Evaluation and Assessment
To gauge the effectiveness of the training program, employers should implement:
- Knowledge Assessments: Tests to evaluate what employees have learned during the training sessions.
- Performance Assessments: Evaluations of employees during emergency response drills to assess their readiness.
4. Continuous Improvement
Regular review and updates to the training program are necessary to keep pace with changing regulations and workplace conditions. Employers should:
- Solicit feedback from employees regarding the training program.
- Stay informed about industry best practices and incorporate them into the training.
Finding the Right OSHA H2S Training Course
Selecting a reputable training provider is crucial to ensure the quality of OSHA H2S training. Here are some tips to consider when searching for the right course:
- Verify Credentials: Ensure the training provider is accredited and recognized by OSHA.
- Course Material Quality: Review the course materials to ensure they are detailed, comprehensive, and relevant.
- Training Format: Decide whether in-person training or online training meets your organization's needs best.
- Feedback and Reviews: Look for testimonials or reviews from previous participants to gauge the training quality.
Conclusion: Prioritizing Safety and Training
In conclusion, OSHA H2S training is not merely a regulatory requirement but a vital component of ensuring worker safety in hazardous environments. The potential consequences of H2S exposure underscore the need for effective training programs that equip employees with the necessary knowledge and skills to protect themselves and their colleagues. By investing in quality training and fostering a commitment to safety, organizations can create a safer workplace, enhance productivity, and ensure compliance with OSHA standards. As such, prioritizing OSHA H2S training is a decisive step toward safeguarding the well-being of all employees operating in high-risk environments.